Understanding the Role of Rotomolding in Custom Plastic Production
Understanding the Role of Rotomolding in Custom Plastic Production
Blog Article
Rotational molding, or Rotomolding, has become a preferred production strategy for creating resilient and high-quality plastic parts. Its unique method, which requires heat and twisting components in the shape, ensures consistently distributed strength and consistency in the final product. That website explores the incredible benefits of Rotational Molding and why it has obtained prominence as a process for making difficult and long-lasting plastic components.
Remarkable Energy with Uniform Wall Thickness
One of many crucial skills of rotomolding lies in its ability to create parts with standard wall thickness. Unlike other manufacturing methods which could keep uneven or slim areas prone to weakness, rotomolding ensures consistency in most layer. By evenly heat and rotating the form, the molten resin flows easily, making easy and robust plastic areas that may tolerate large masses and withstand impact.
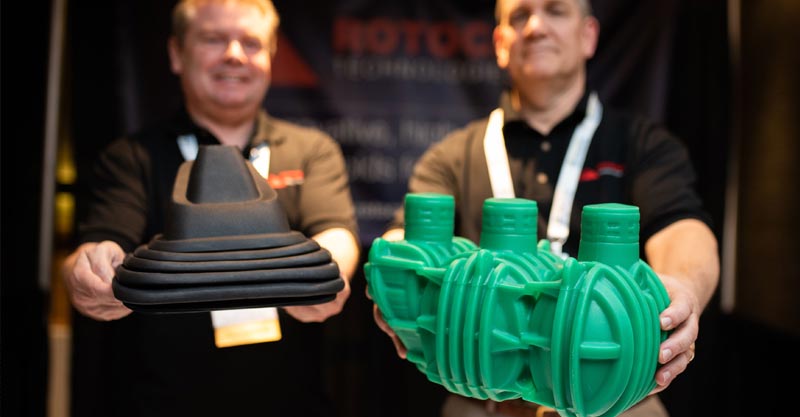
This function makes rotomolded components ideal for purposes requiring architectural strength, such as for instance large tanks, playground equipment, and industrial containers.
Improved Longevity with Stress-Free Molding
Stress can damage plastic pieces, impacting their life and performance. Fortuitously, the rotomolding method removes internal challenges often found in different molding techniques. Because no high-pressure makes are utilized during production, the plastic material activities little pressure, resulting in a more durable solution that performs easily over time.
Moreover, the absence of joints or weld lines enhances the overall longevity of rotomolded pieces, creating them resilient to cracking, dividing, and environmental use and tear.
Exceptional Flexibility and Customization
Rotomolding offers unmatched design flexibility, allowing producers to generate complicated patterns and structures with precision. The ability to incorporate added functions like bones, inserts, or consistency guarantees that the final item meets specific practical or visual requirements.
This technique also supports the use of a wide selection of components and additives, such as for example UV stabilizers and colorants, further improving toughness by making pieces immune to facets like sunlight exposure, fading, and substance damage.
Resilience in Intense Conditions
Rotomolded parts are developed to last, even if confronted with serious environments. They keep their strength in tough temperatures, withstand corrosion from compounds, and experience prolonged outside use. That makes them especially valuable in industries like agriculture, structure, and marine purposes, where components experience difficult conditions daily.

Their power to perform dependably in such environments decreases the requirement for regular substitutes, making rotomolded areas equally cost-effective and sustainable.
Operating the Potential of Durable Parts
The raising need for trusted and tough plastic pieces remains to place rotomolding at the front of manufacturing innovation. With its detail, stress-reducing benefits, and ability to withstand diverse settings, rotomolding is shaping the way in which industries prioritize power and durability within their products. By investing in that sophisticated method, suppliers may generate plastic pieces that stay the check of time.
Report this page