The Future of Automated Ship Loading Systems
The Future of Automated Ship Loading Systems
Blog Article
The Future of Automated Ship Loading Systems
Choosing the right ship running system is a crucial part of ensuring bucket wheel excavator interface procedures, charge management, and the secure managing of materials. With different possibilities, choosing the one that aligns with your certain needs can feel overwhelming. That manual can go you through necessary facets to consider before generally making your decision.
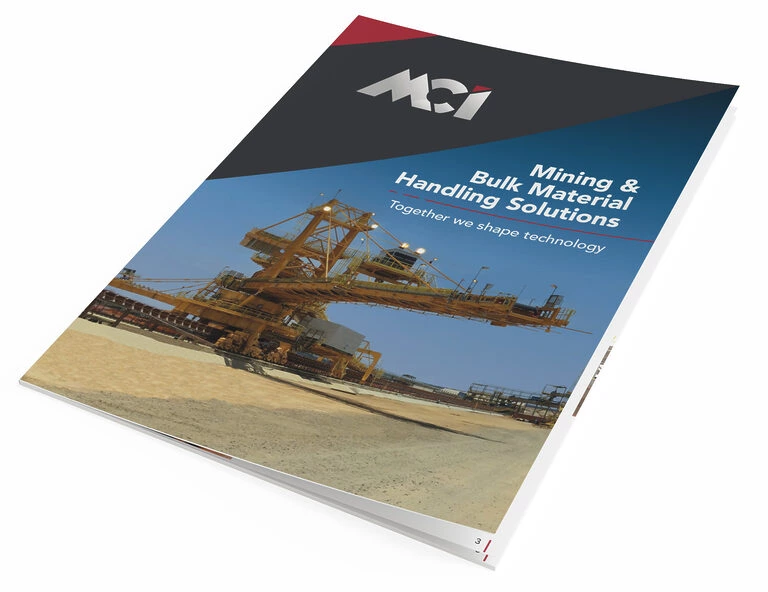
Realize Your Material Handing Requirements
The type of product being treated deeply influences the decision of vessel packing equipment. For instance:
Dry volume objects (like feed or cement) might need enclosed conveyor strip programs to reduce wastage and environmental impact.
Wet or sticky components, such as for example slurry, necessitate unique managing systems to prevent clogging.
Hazardous products require programs with additional safety and containment functions to comply with regulatory standards.
Prior to making a decision, categorize your components and assess their bodily attributes, such as for instance compound size, humidity material, and flowability.
Examine Volume and Throughput
Every ship filling operation is unique in their range and demand. Establish your throughput requirement in tons hourly to measure the system's capacity. A method that suits (or slightly surpasses) your capacity needs assures optimal operations without overburdening equipment.
For high-capacity needs, long-term efficiency often outweighs larger original costs. For smaller loads, a more compact and economical program may suffice. Ensure the system are designed for maximum functional situations without reducing their performance.
Prioritize Environmental Criteria
Environmental sustainability is becoming more important in vessel filling operations. Several programs today come designed with characteristics that reduce dust, sound, and emissions. Look for:
Dust control programs to prevent substance reduction and minimize health problems for operators.
Energy-efficient styles to reduce operational prices and carbon footprints.
For regions with strict environmental rules, prioritizing sustainability can avoid fines and improve your company's reputation.
Give attention to Mobility and Customization
Ports usually handle diverse components or ships of varying sizes. A variable vessel packing system that may conform to adjusting demands is really a smart investment. Look for programs with:
Adjustable configurations (e.g., extendable conveyors or variable growth lengths) for improved versatility.
Modular parts to modify and update the system as needed.
Such features increase long-term electricity and decrease the likelihood of needing a complete process overhaul in the future.
Contemplate Easy Maintenance
Downtime could be expensive. Opt for techniques developed with ease of maintenance in mind. Functions like quick-access factors, quickly replaceable parts, and modern diagnostics tools reduce restoration situations and help identify potential problems before they occur. Preventive preservation options may also extend the system's life and maintain efficiency.
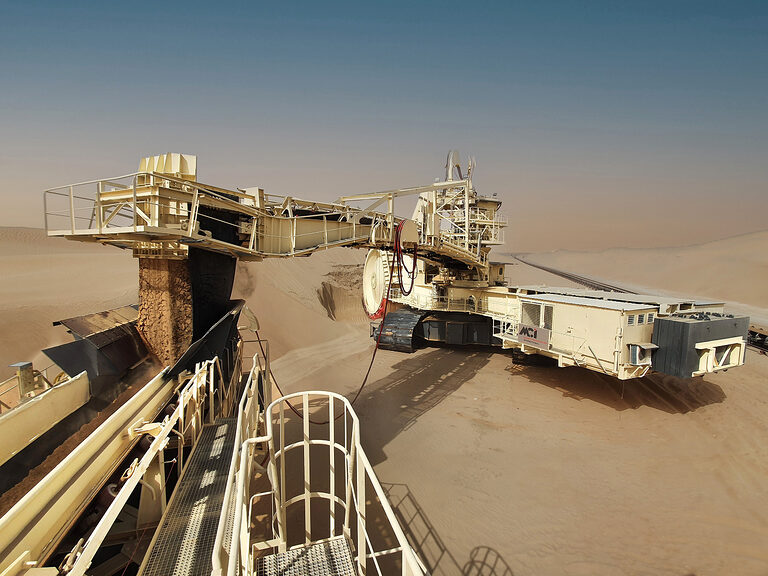
Think Forward About Automation
Automation is fast transforming the delivery and logistics industry. Contemporary vessel launching programs often contain computerized controls for greater detail, reduced human mistake, and increased safety. While it might involve a greater upfront cost, automation often reduces long-term job costs and improves working reliability.
Final Ideas
Choosing a ship launching program isn't pretty much the equipment's technical specs. It's about aiming the system with your operational wants, environmental standards, and potential scalability. By understanding your requirements and prioritizing key characteristics, you'll choose process that helps your operations for a long time to come. Report this page